Propulser les immenses mouvements de creusement et de levage des excavatrices modernes nécessite un réseau complexe de machines hydrauliques fonctionnant en coordination précise.. At the heart of these systems lie the hydraulic cylinders responsible for actuating each articulating movement. Let’s examine the engineering behind these vital components.
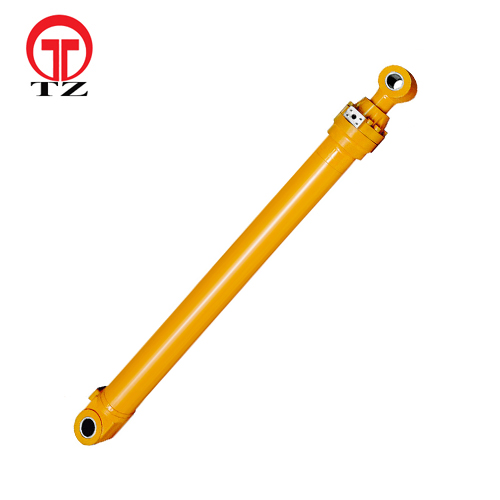
Cylinder Design
Excavator cylinders resemble traditional hydraulic cylinders but on an outsized scale. Diameters range from 3-12 inches with strokes extending 6-72 inches depending on machine size. Heavy- duty construction utilizes hardened chromed or polished tubing reinforced longitudinally by welded gussets or ribbing for operational strength. Cylinders pivot or slide within robust mounting points. Seals prevent pressurized oil leakage maintaining smooth motion.
Actuation Methods
Several excavator part hydraulic cylinder work in concert to manipulate the arm, dipperstick and bucket. Single-acting cylinders only push during extension requiring a return spring. Double-acting valves rapidly control pressure in both expansion and retraction strokes approaching a hydraulic actuator’s maximum force output for strength-intensive tasks.
Trip valves protect equipment by safely cushioning movement exceeding pressure limits preventing damage from overloading or collisions. Proportional directional control valves precisely meter hydraulic flow for smooth coordinated multi-cylinder motions.
Maintenance Considerations
Cleaning and lubricating rod and tube surfaces regularly prolongs seal lifespan removing contaminants. Sensors monitor pressure dips indicating internal seal wear requiring replacement before total failure occurs. Rebuilds involve disassembly, inspection and replacement of all seal components.
Common Issues
Over pressurization beyond rated specs risks tube or rod damage and leakage. Contamination leads to accelerated seal deterioration necessitating more frequent rebuilds. Impact dents compromise structural integrity necessitating replacement. Extreme temperatures affect oil viscosity and seal elasticity. Corrosion shortens service intervals requiring protective coatings.
Fitting Repairs
Burst hoses necessitate crimped replacement with appropriate pressure and bend radius ratings. Damaged fittings installing cylinders require hardware matching machine specifications for structural integrity. Alignment ensures focused force application avoiding unnecessary stresses.
With careful monitoring, scheduled maintenance optimizes availability and prevents catastrophic failures endangering operators. Proper specifications combined with trained installation yield long component lifecycles from robust excavator hydraulic systems.